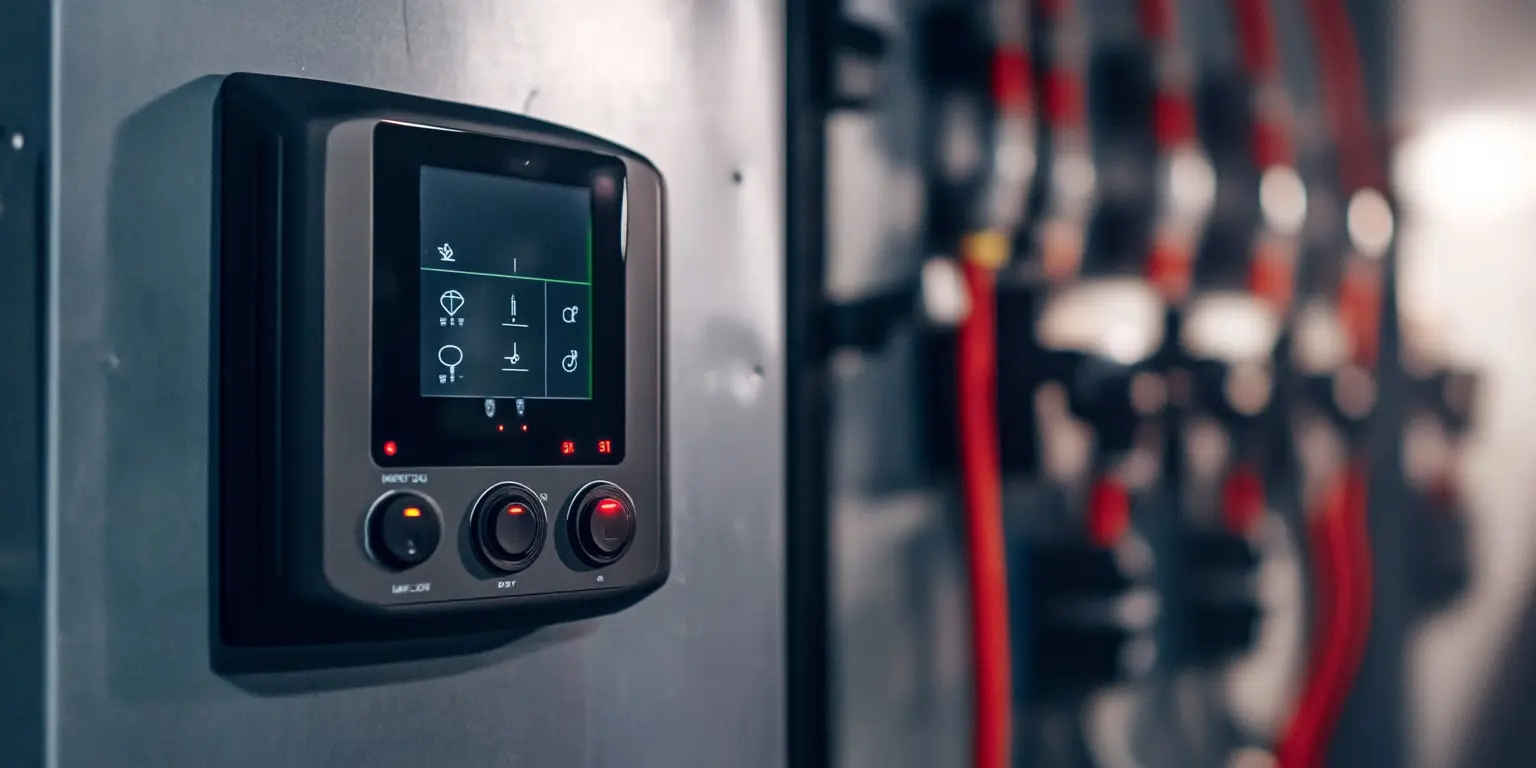
How to Stay Compliant with Equipment Tracking in the Energy Sector
Table of Contents
- Introduction
- Why Compliance is Critical in Equipment Tracking
- Key Regulations Impacting Equipment Tracking in the Energy Sector
- Challenges in Equipment Tracking
- Best Practices for Staying Compliant
- Leveraging Technology for Effective Equipment Tracking
- Benefits of Compliance in Equipment Tracking
- Conclusion
Introduction
The energy sector is one of the most highly regulated industries globally. From oil and gas to renewable energy, companies must adhere to a myriad of regulations that govern their operations. Equipment tracking is a cornerstone of these regulatory frameworks, as it ensures operational safety, efficiency, and environmental compliance.
In this blog post, we’ll explore why compliance in equipment tracking is critical, examine the key regulations that impact the energy sector, and provide actionable strategies for staying compliant.
Why Compliance is Critical in Equipment Tracking
Operational Safety and Risk Management
Accurate equipment tracking minimizes the risk of accidents and ensures that all tools and machinery are in proper working condition. This is crucial in high-risk environments like offshore rigs or wind farms, where equipment failure can lead to catastrophic outcomes.
Environmental Stewardship
Regulatory agencies often require companies to monitor and report the usage and maintenance of their equipment to minimize environmental harm. Non-compliance can lead to significant fines and damage to a company’s reputation.
Financial Implications
Non-compliance can result in hefty fines, legal action, and operational downtime. Effective equipment tracking mitigates these risks by ensuring adherence to regulations and maintaining operational continuity.
Key Regulations Impacting Equipment Tracking in the Energy Sector
OSHA (Occupational Safety and Health Administration)
In the United States, OSHA sets strict standards for workplace safety, including equipment maintenance and usage logs. Companies must ensure their tools and machinery meet OSHA requirements to avoid penalties.
EPA (Environmental Protection Agency)
EPA regulations often require detailed tracking of equipment to monitor emissions and environmental impact. This includes monitoring the condition of pipelines, valves, and other critical components.
International Standards
For companies operating globally, ISO standards like ISO 14001 (Environmental Management Systems) and ISO 45001 (Occupational Health and Safety) provide frameworks for equipment tracking compliance.
Challenges in Equipment Tracking
Scale and Complexity
Large-scale energy operations involve thousands of pieces of equipment, often distributed across multiple locations. Tracking each item manually is impractical and prone to errors.
Regulatory Overlap
Navigating overlapping regulations from multiple governing bodies can be complex. Companies must ensure compliance with local, national, and international standards.
Technological Barriers
Legacy systems and outdated tracking methods often hinder effective compliance. Companies must upgrade to modern, scalable solutions.
Data Accuracy
Inaccurate or incomplete tracking data can lead to compliance breaches. Ensuring data accuracy requires robust processes and tools.
Best Practices for Staying Compliant
Implement Standard Operating Procedures (SOPs)
Develop comprehensive SOPs for equipment tracking, including guidelines for usage, maintenance, and inspections. Ensure these procedures are regularly updated to reflect regulatory changes.
Conduct Regular Audits
Frequent audits help identify gaps in compliance and tracking. Use these audits to review data accuracy, maintenance schedules, and equipment conditions.
Train Employees
Invest in training programs to educate employees about the importance of equipment tracking and compliance. This ensures that everyone from field technicians to office staff understands their role in maintaining compliance.
Centralize Data Management
Use a centralized system to store and manage equipment data. This makes it easier to access information for audits and reporting.
Leveraging Technology for Effective Equipment Tracking
IoT and Sensors
The Internet of Things (IoT) enables real-time tracking of equipment using sensors. These sensors can monitor location, usage, and condition, providing actionable insights.
RFID and Barcode Systems
RFID tags and barcodes simplify the tracking process by enabling quick scanning and inventory management. These technologies are particularly useful for large-scale operations.
Digital Twin Technology
Digital twins create virtual models of physical equipment, allowing companies to simulate performance, predict failures, and optimize maintenance schedules.
Cloud-Based Platforms
Cloud-based tracking systems offer scalability and real-time access to data, ensuring that all stakeholders are aligned on compliance requirements.
Benefits of Compliance in Equipment Tracking
Enhanced Safety
Compliance ensures that equipment is maintained and used safely, reducing the risk of accidents and injuries.
Operational Efficiency
Accurate tracking minimizes downtime by enabling proactive maintenance and efficient resource allocation.
Cost Savings
Avoiding fines, legal action, and equipment failures translates into significant cost savings for companies.
Improved Reputation
Demonstrating compliance boosts credibility with regulators, stakeholders, and the public.
Conclusion
Staying compliant with equipment tracking in the energy sector is a multifaceted challenge that demands a proactive approach. By understanding the regulatory landscape, adopting best practices, and leveraging modern technology, companies can ensure operational safety, minimize risks, and maintain their competitive edge. Compliance isn’t just a regulatory necessity—it’s a strategic advantage in an increasingly complex and demanding industry.